Market Intelligence
Our understanding of today’s consumer brands equip us to positively impact their businesses. This is why our first priority when we engage with a customer is to align ourselves by understanding their business, the brand and the sales objectives. Because we view our customers’ challenges as our own, we want to offer solutions and options.
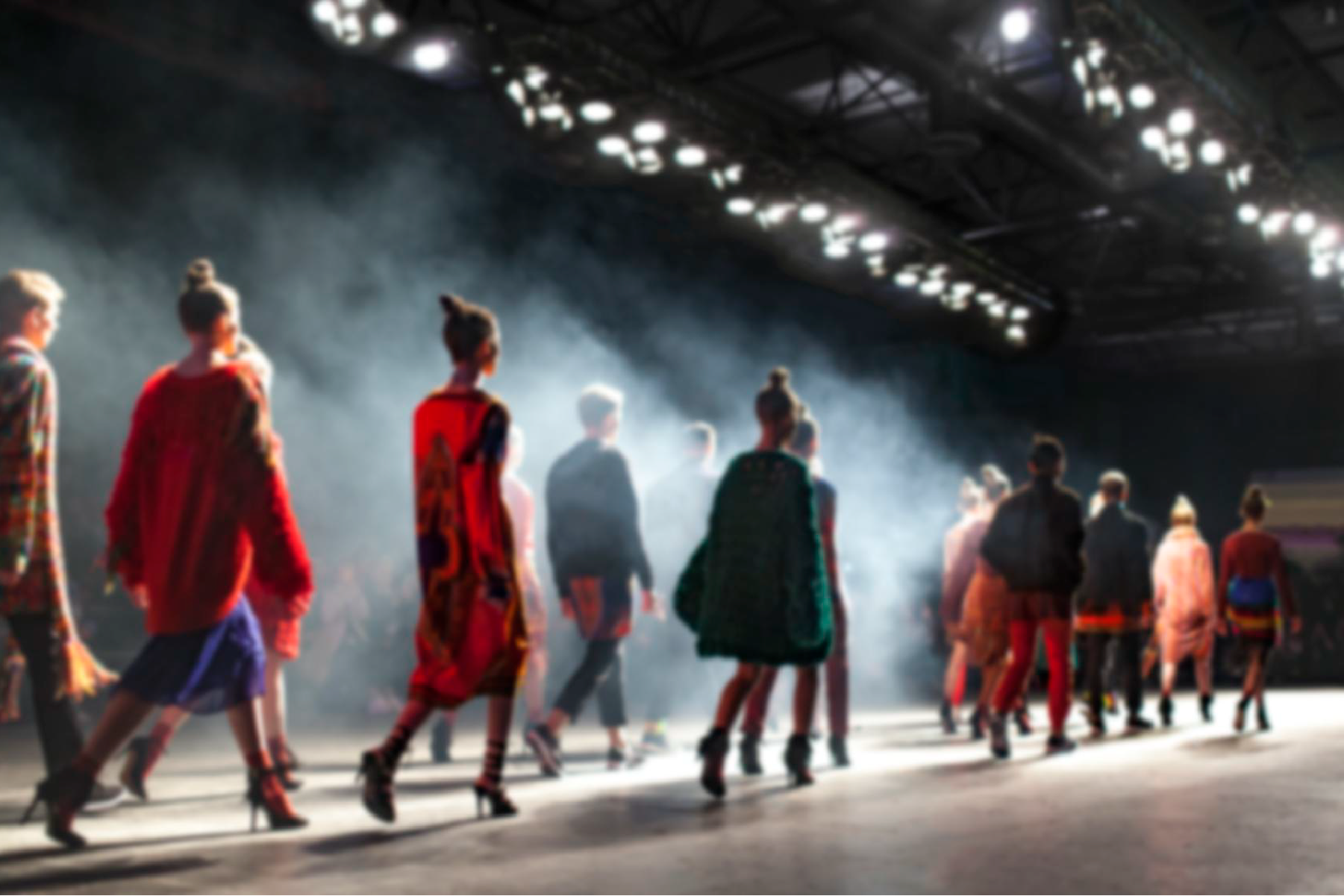
Concept and R&D
Our dedicated Raw Materials Team is constantly meeting with suppliers and fabric mills while also attending the latest trade shows to gather market insights. With our understanding of our customers' needs, our dedicated R&D teams are able to bring solutions to our customers with respect to innovative fabrications, trim, and manufacturing techniques. <br> <br> We are able to provide support in concept development as well as key product development, including custom fabric development.
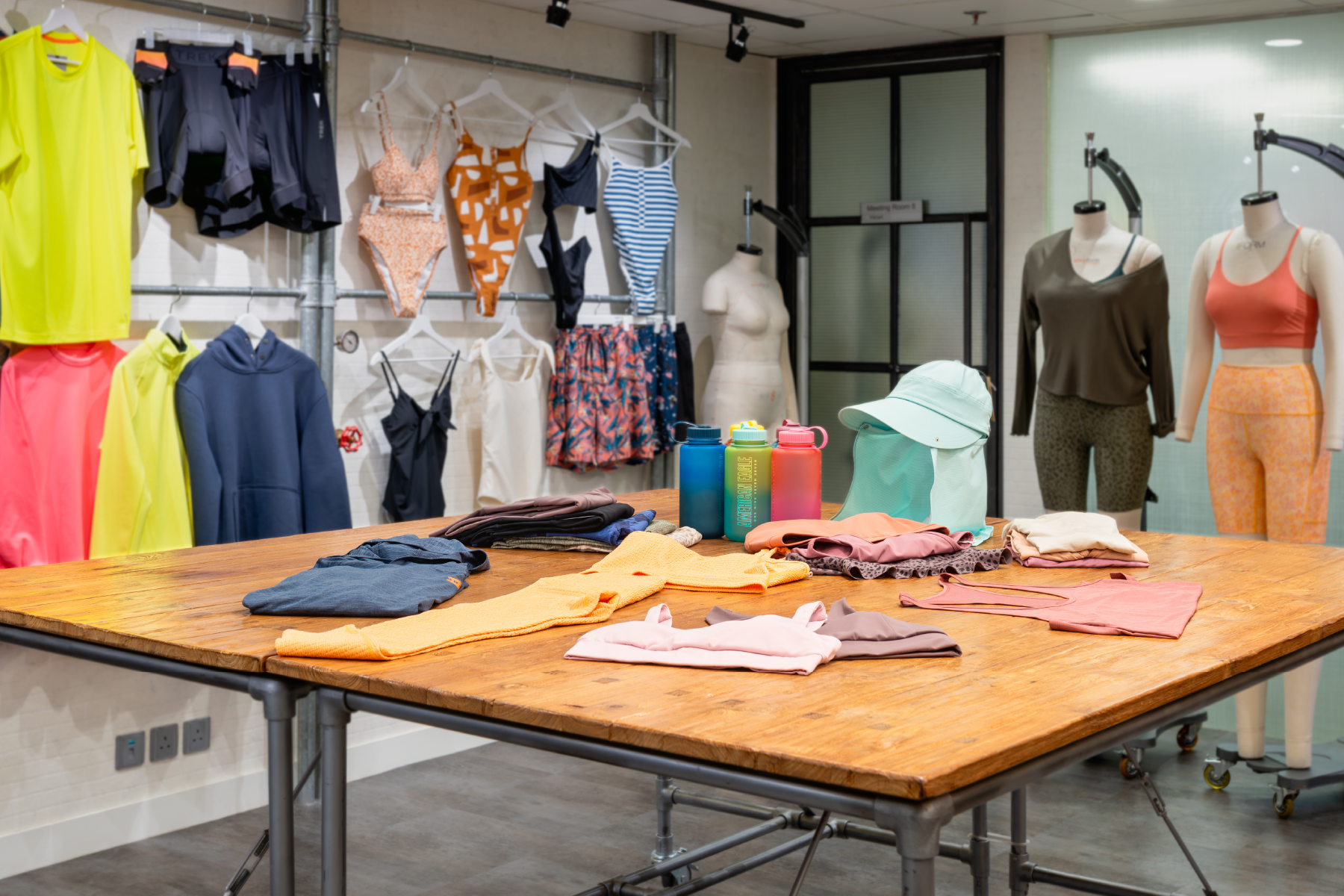
Design & Product Development
Led by our creative director of 20 years’ experience, product design and development is an essential part of our GTM solution, enabling us to deliver quality products to our customers and add value to their brands. Our team of eight in Hong Kong and the US provides comprehensive support to customer design teams, from establishing style preferences and budgets to originating new designs using industry-specific software and providing 3D virtual samples. <br>Our US Design Studio works closely with customers on creating clear, detailed 3D visualizations, reducing the need for many samples and significantly shortening the lead time in product development. The team’s software skills include CLO, Browzwear, Shimasaki, and Xtex. <br> <br> Experts from our Tech Support Team perform garment engineering, technical support, fitting support and pattern development, enhancing quality and fit consistency. Experienced on-site specialists in Hong Kong and the US with strong wet-processing knowledge support and enhance design and development decisions
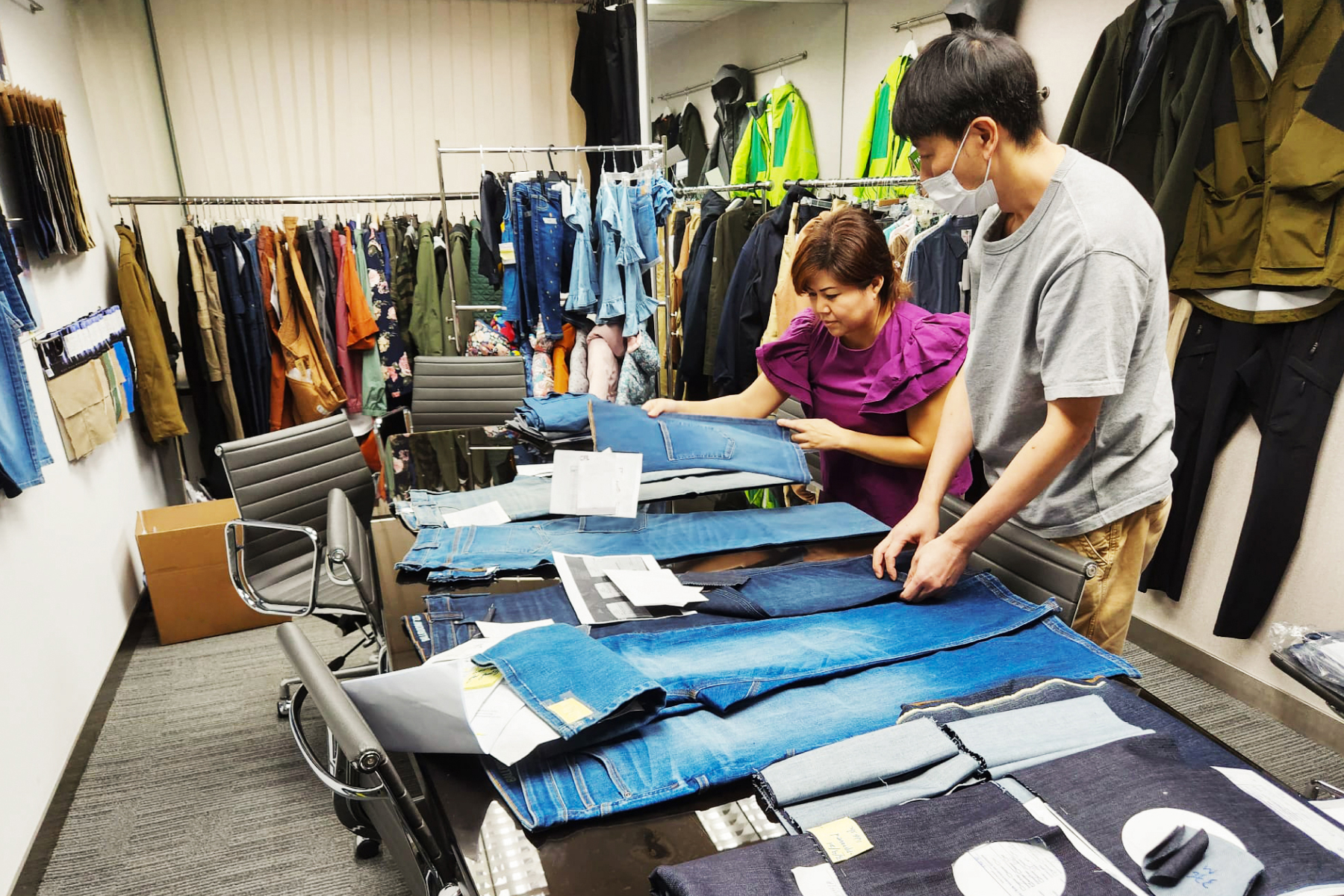
Raw Materials & Production Management
Managing the raw material sourcing from the development stage through to production, examining and verifying crucial details like fiber content, yarn count and weight of the procured raw materials before the first cut is the raison d’être of the Tech Support Team. <br> <br> Collaboration between our Tech Support and manufacturing partners’ technical support teams in information sharing and best practices means CFL is kept abreast of the latest trends and techniques in equipment upgrades, manufacturing processes, and wet and dry processing applications. Mutually beneficial, knowledge refreshes keep these key partnerships strong. Tech Support also constantly explores new technologies and eco-friendly chemical options. <br> <br> Meanwhile the merchandising team connects with design and development colleagues to understand the specifics of the raw materials required for the garments, and works with the factories to ensure all specifications are met throughout the sourcing process.
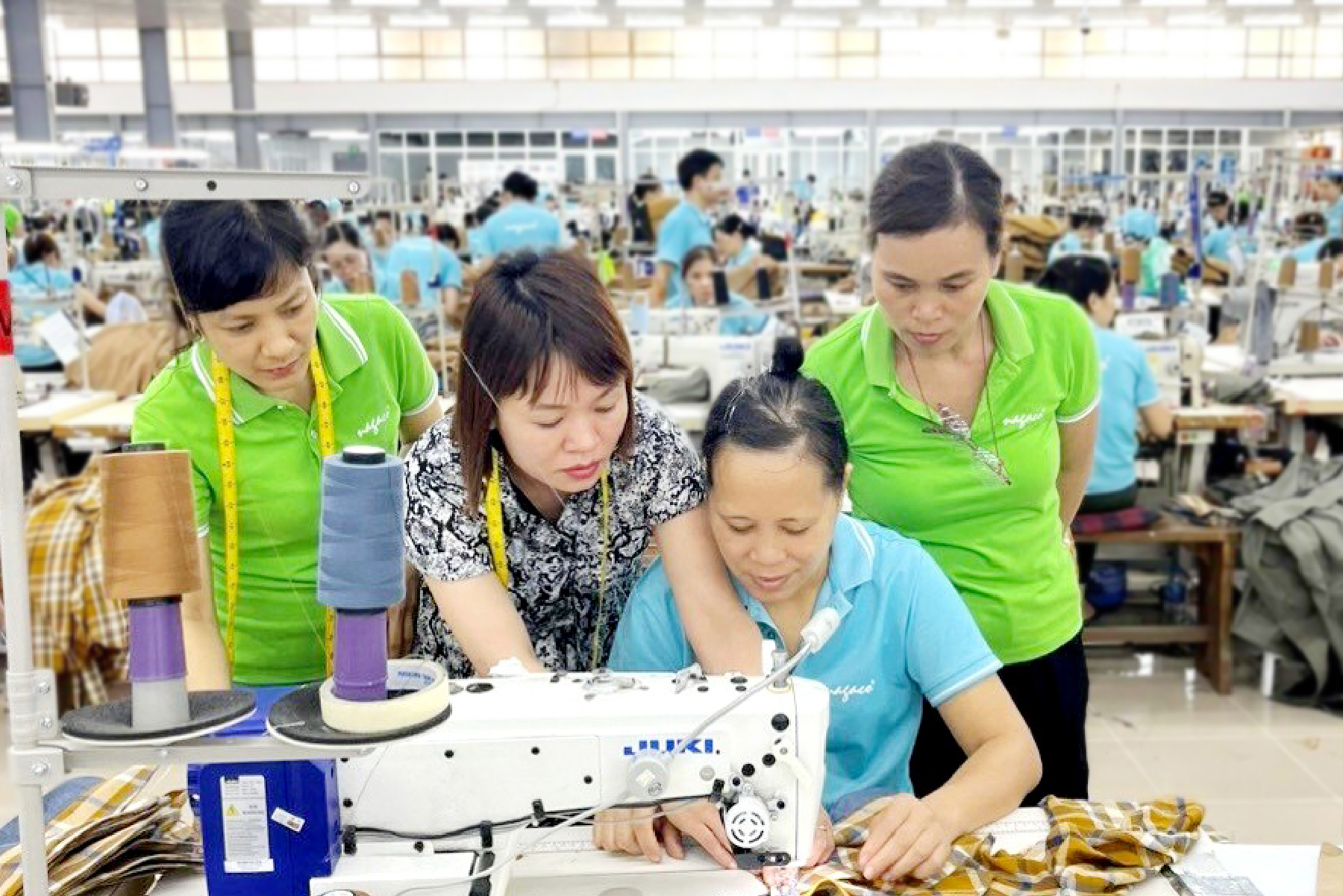
Quality Control & Testing
We recognise that delivering quality products to our customers is fundamental to our commitment to them — basically delivering on what was promised. Many of the brands we work with do not have on the ground QC visibility of their products. We do, because delivering the product we promised is just as important to our success as it is to our customers. We are known for our track record of reliability and enviable low return rate. <br> <br> Our group of QC professionals, using their manufacturing experience, conducts a detailed process of checks and balances for each order, from pre-production meetings through to final inspection. Off-shore teams are based close to the manufacturing facilities to conduct on-site inspections during production to monitor performance, including in-line inspections on semi-finished products to ensure quality, and to execute functionality tests on production samples to ensure they are fit for purpose. Many on the Team are experts, including certified colorists, wet processing specialists and technical engineers. <br> <br>They understand very well the individual customer quality requirements and how crucial it is to implement critical process controls to ensure product quality consistency. That needs buy-in from manufacturing partners to ensure expectations are met, and with an emphasis on prevention before production we provide comprehensive training support — so we can “get it right the first time” for high fulfilment and delivery performance.
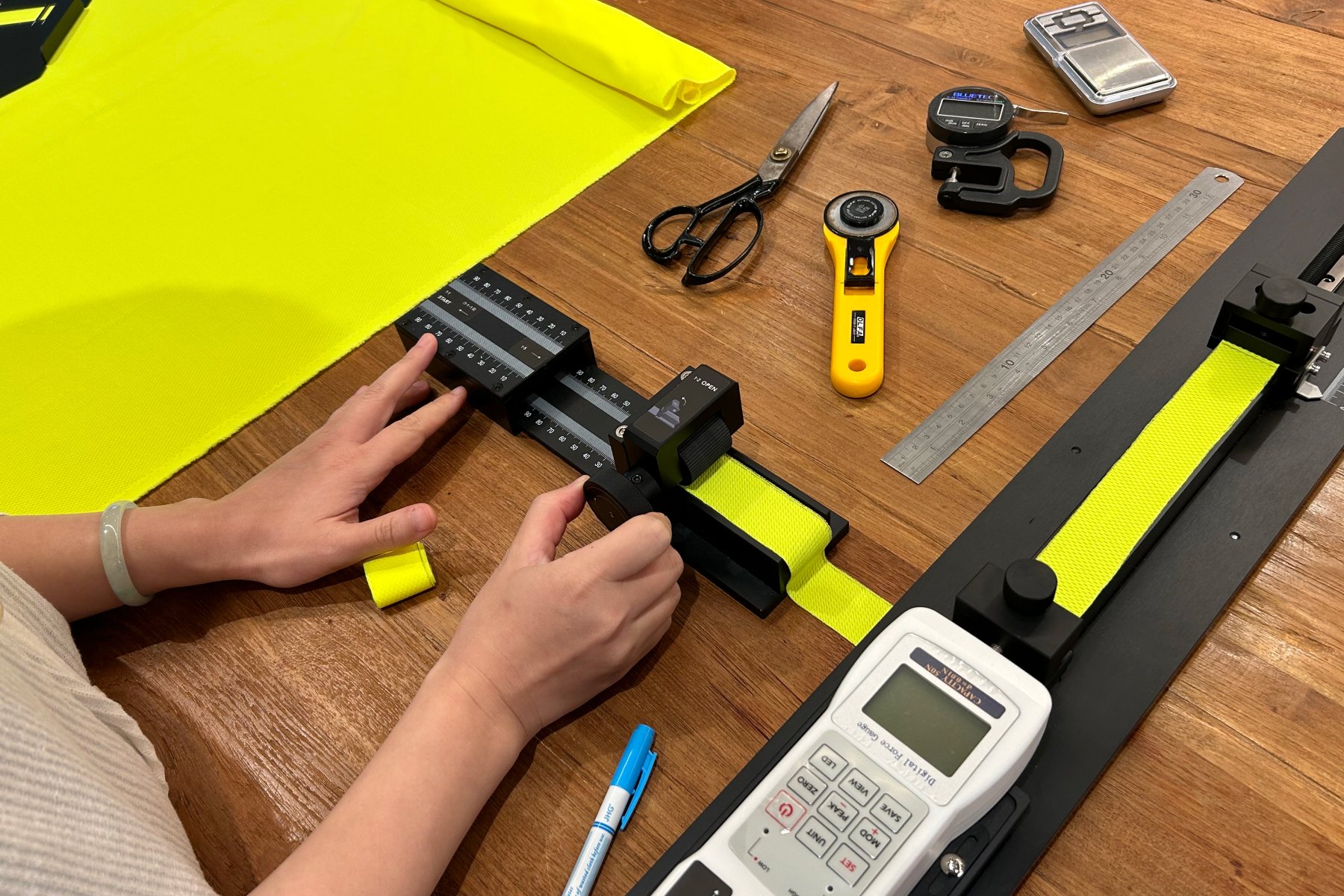
Supply Chain Management
We operate within a modular system so customers can choose to engage in any or all of our GTM Solution services. We take our initial brief from meeting with a customer, and conduct our own market intelligence to analyze and fully understand what is required. Then we offer tailored solutions, customized to tackle specific customer needs, so that the customer can focus their resources on developing their brand and making sales. <br> <br> Our GTM Solution ranges from product design and raw material sourcing, to technical package development and sample development, and from material procurement and sourcing of contract factories, to production, quality control, and logistics and customs clearance services.
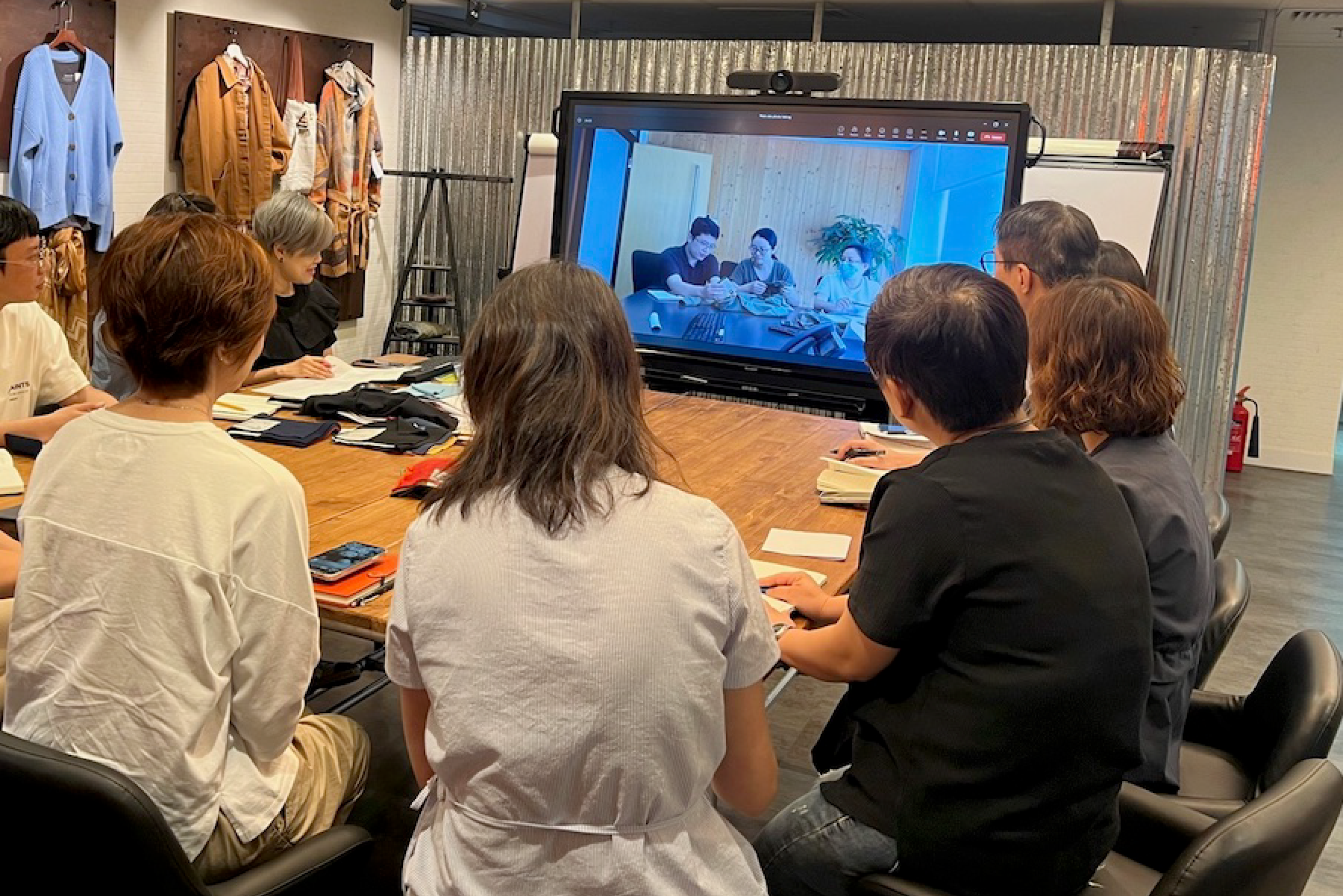
Global Logistics Management
We maintain a tried and tested network of international forwarders, liners, and domestic carriers to ensure prompt, compliant and cost-effective shipments and deliveries to customers. This involves over 30 years of in-depth knowledge of international trade and US Customs rules from a team of import/export specialists to ensure proficient customs clearances and transfers, and experience in dealing with any customs rulings, challenges or interpretations of requirements.
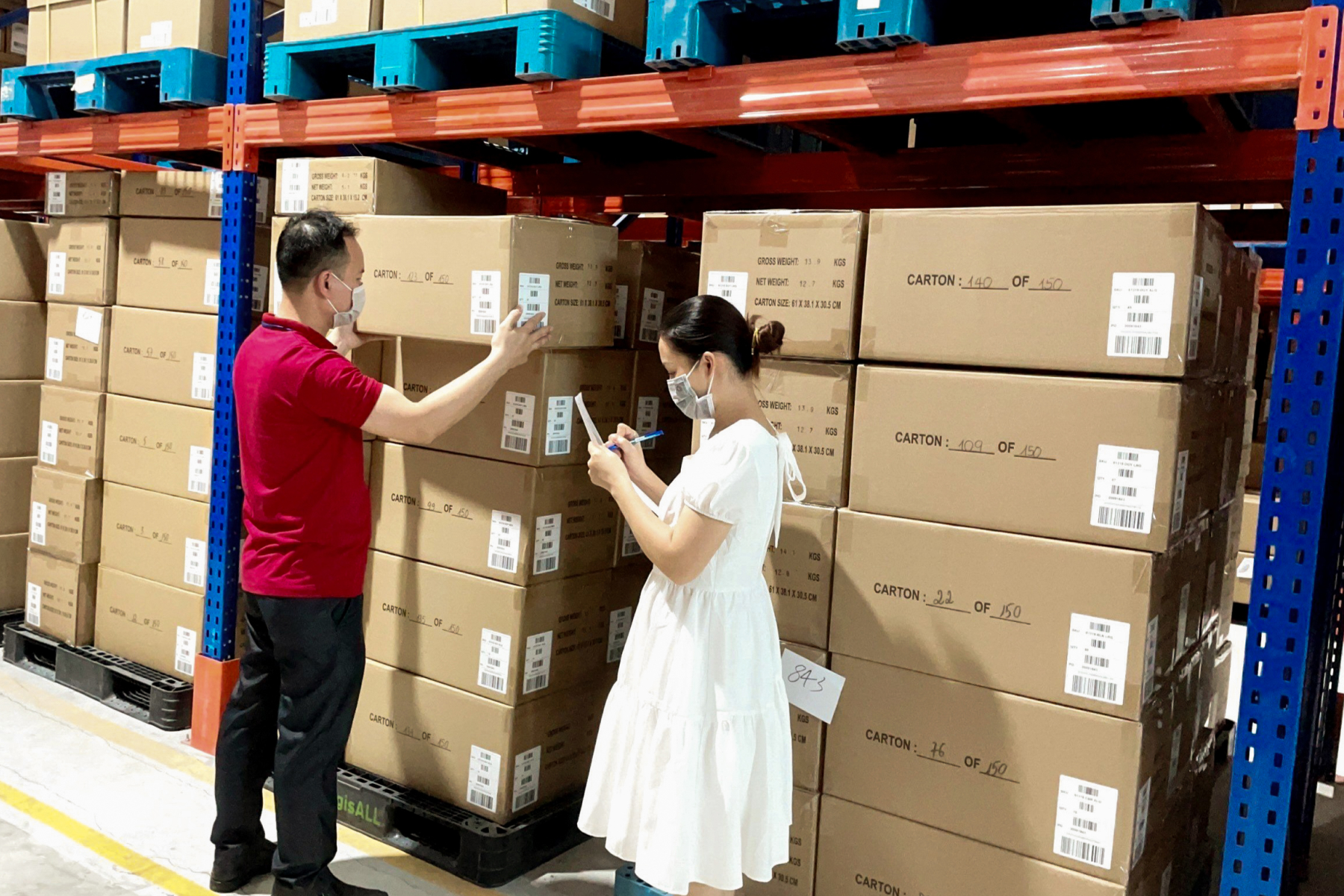